Druk przestrzenny w przemyśle kosmicznym. Jak daleko zaszliśmy? [ANALIZA]
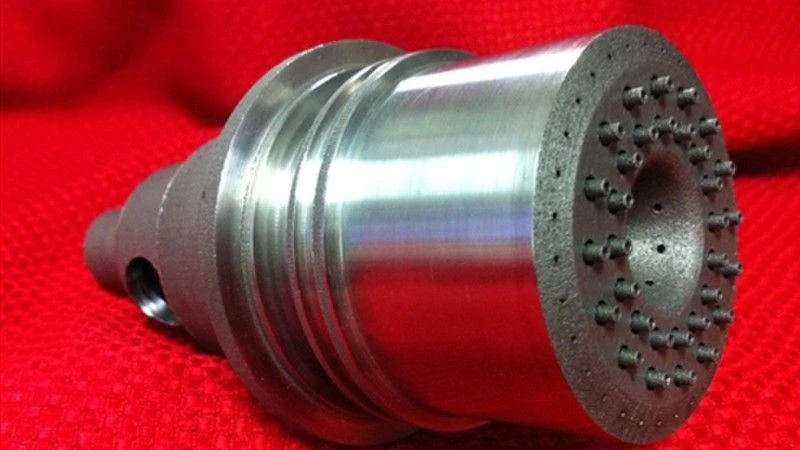
Technologie wytwarzania przyrostowego zaliczają się do tych specyficznych gałęzi rozwoju przemysłowego, z którymi wiązane są duże nadzieje na kolejny krok milowy w eksploracji kosmosu. Optymizmem napawają przede wszystkim dokonania w zakresie addytywnej produkcji syntetycznych podzespołów rakiet nośnych oraz precyzyjnych instrumentów na potrzeby pozaziemskich misji naukowo-badawczych. Niemniej jednak oczekiwania co do dalszych postępów w tej materii wybiegają już znacznie dalej, a ich hipotetycznym rozwinięciem są nierzadko wizje orbitalnych manufaktur satelitarnych oraz autonomicznie budowanych habitatów planetarnych.
Przełom na styku branż
Imponujące tempo rozwoju technik wytwarzania przyrostowego, zwanego też drukowaniem przestrzennym (ang. 3D printing), notowane jest w wielu obszarach zastosowań użytkowych – począwszy od produkcji urządzeń mechanicznych i elektronicznych, poprzez budownictwo i modelowanie komputerowe, aż po inżynierię materiałową i biotechnologię. Branża kosmiczna nie jest tutaj wyjątkiem, przy czym jej udział w generowaniu innowacji na polu technologii addytywnych jest zaliczany do tych najbardziej znaczących. Sprzyja temu swego rodzaju sprzężenie zwrotne, w ramach którego doskonalenie metod drukowania przestrzennego staje się dla podmiotów sektorowych sposobem na zniwelowanie uciążliwych barier dostępu do rynku i samej przestrzeni pozaziemskiej.
Choć nawiązanie ściślejszej relacji branżowej nastąpiło stosunkowo niedawno (bezpośrednio w drugiej dekadzie XXI wieku) i wciąż nabiera kształtu, sektor kosmiczny zdążył już znaleźć komercyjne zastosowanie dla zaawansowanych technologii addytywnych. Pierwsze przemysłowe wzorce ich wykorzystania wypracowywano w dużej mierze w korelacji z pokrewnym sektorem aeronautycznym, dzieląc dążenie do opanowania przyrostowych metod wytwarzania podzespołów napędowych. W krótkim czasie wymiar ten rozszerzono o bardziej rozbudowane, zintegrowane mechanizmy, co skutkowało radykalnym zmniejszeniem ilości osobnych części, a tym samym uproszczeniem linii produkcyjnej i znacznym obniżeniem kosztów produkcji silników. Spadła przy tym ilość łączeń i spawów osłabiających w ogólnym rozrachunku spajaną w ten sposób konstrukcję.
Jednym z głównych kamieni milowych tego procesu był projekt uruchomiony w 2012 roku przez wydział lotniczy koncernu General Electric (GE Aviation) we współpracy z Morris Technologies. Postawiono sobie wówczas za cel kompleksową ocenę potencjału wdrożenia technologii addytywnych do seryjnej produkcji silników samolotowych. Wyniki tych prac były na tyle obiecujące, że z miejsca podjęto decyzję o uruchomieniu na szeroką skalę wytwarzania przyrostowego wybranych podzespołów. Jednym z nich był nowy syntetyczny mechanizm wtryskiwacza paliwa, redukujący ilość stosowanych dotychczas pojedynczych części z 20 do jednej (!), a przy tym posiadający o blisko 25 proc. mniejszą masę od swojego klasycznego, składanego odpowiednika.
Dalsze postępy w badaniach GE Aviation doprowadziły do ogólnej zmiany spojrzenia na produkcję napędów samolotowych tej firmy. Najbardziej aktualnym tego przejawem stał się zmodyfikowany model lekkiego silnika turbośmigłowego, w którym pochodzące od różnych dostawców 855 osobnych części zostało zastąpione… 12 zintegrowanymi podzespołami. Zaprezentowaną w styczniu 2018 roku jednostkę napędową (efekt pracy 400 inżynierów GE, w tym z zakładów koncernu w Polsce) złożono w ponad 1/3 z elementów „drukowanych”, dzięki czemu silnik okazał się lżejszy od swoich klasycznie montowanych odpowiedników o ponad 45 kg. Jednoczesny wyraźny skok odnotowano w parametrach osiągów: napęd wytworzonych w technologii przyrostowej zyskał 10 proc. mocy, zapewniając przy tym o 20 proc. wydajniejsze spalanie paliwa. Oprócz tego, znacząco uproszczono i skrócono czas obsługi montażowej i serwisowej silnika.
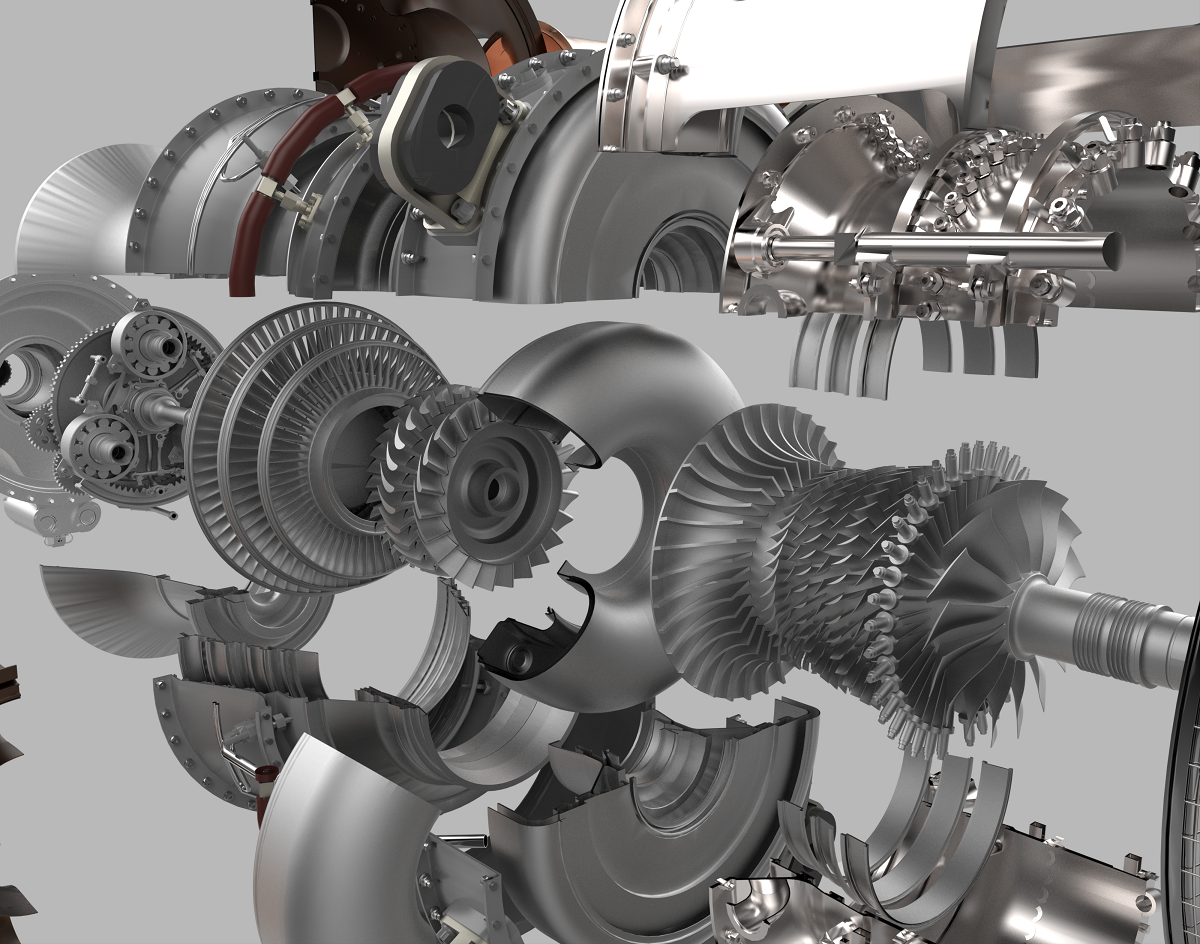
Kosmos a technologie addytywne: szybciej – taniej – łatwiej?
Niekwestionowane korzyści z zastosowania technologii addytywnych w wytwarzaniu silników lotniczych stały się swego rodzaju obietnicą dalszych postępów na tej ścieżce w branży kosmicznej. Czerpaniu z doświadczeń aeronautycznych sprzyjały pokrewne wysokie standardy i restrykcyjne wymogi co do precyzji wytwarzania i oczekiwanej odporności materiałowej syntetycznych podzespołów. Akceptowalny poziom dostosowania zapewniło wdrożenie precyzyjnych metod łączenia metalicznych materiałów czynnych, stosując stapianie z użyciem wiązki elektronów lub lasera (EBM - Electron-Beam Melting, DMLM - Direct Metal Laser Melting). Techniki te pozwoliły na uzyskiwanie ultra cienkich warstw stopu (rzędu 40-20 mikronów, czyli cieńszych od ludzkiego włosa). Te z kolei okazały się niezbędne dla zapewnienia odpowiednio odpornego łączenia i zwartości struktury narażonej na wysokie obciążenia.
W warunkach kosmicznych jednak nawet i tak zaawansowane metody wytwarzania nie zawsze odpowiadają wymaganiom (ewentualnie, nie domykają całego spektrum zapotrzebowania). Stąd agencje i instytuty kosmiczne na całym świecie intensywnie pracują nad rozwinięciem dedykowanych technologii addytywnych, dostosowanych do ściśle przypisanych sytuacji. Dłuższą historią swojego zaangażowania w tym zakresie może poszczycić się ośrodek NASA Marshall Space Flight Center, działający w Huntsville w stanie Alabama, który podjął się równoległych badań w kilku obszarach rozwoju drukowania przestrzennego.
Czytaj też: Druk 3D w produkcji satelity USAF
Te najbardziej wczesne nie dotyczyły jeszcze wytwarzania mechanizmów napędowych, gdyż miały one pojawić się jako realna alternatywa dopiero kilka lat później. W pierwszej kolejności NASA Marshall Space Flight Center zajęło się wspieraniem prac i badań (głównie zewnętrznych) w zakresie wykorzystania druku przestrzennego w konstrukcjach satelitarnych. Szczególną uwagę poświęcono tworzeniu demonstratorów technologicznych i polimerowych modeli lekkich satelitów (głównie typu CubeSats), sprawdzając stopniowo ich możliwości działania na orbicie. Jeden z pierwszych tego typu przypadków miał miejsce w 2005 roku za sprawą projektu realizowanego przez Utah State University, gdzie stworzono innowacyjny prototyp mikrosatelity opartego na platformie wykonanej w technologii addytywnej. Zapoczątkowana wówczas ścieżka doprowadziła m.in. do rozpoczęcia w listopadzie 2017 roku misji satelity Tubesat-POD (TuPOD), pierwszego obiektu stworzonego w całości w procesie wytwarzania przyrostowego, który umieszczono na orbicie z pokładu Międzynarodowej Stacji Kosmicznej (ISS).
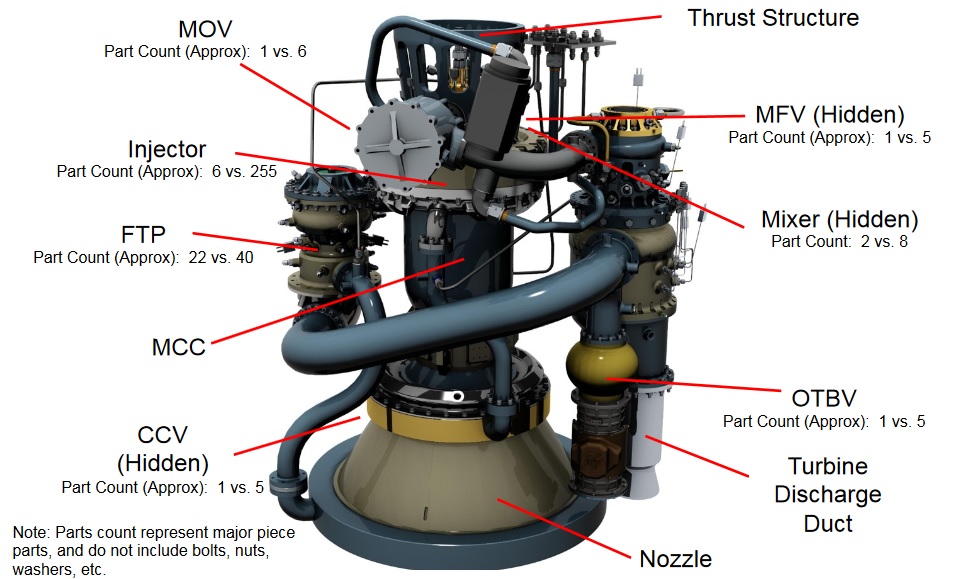
W zakresie konstrukcji napędowych rakiet nośnych naukowcy NASA wytworzyli m.in. funkcjonalny, spełniający rygorystyczne standardy mechaniczne i temperaturowe prototyp dwuczęściowego wtryskiwacza paliwa, przygotowanego na wzór instrumentu współpracującego z silnikami RS-25 (dedykowanymi obecnie rakiecie SLS), a składanego dotychczas ze 163 osobnych części. Działanie mechanizmu potwierdzono w trakcie prób przeprowadzonych w sierpniu 2013 roku, włączając w to gorący rozruch silnika zaopatrzonego w to rozwiązanie. Zastosowanie „drukowanego” podzespołu pozwoliło wydatnie skrócić czas produkcji i instalacji systemu.
Dalsze zaangażowanie ośrodka NASA z Huntsville w tej dziedzinie przyniosło finalnie (marzec 2018 roku) kolejny kamień milowy w postaci stworzenia nowej dyszy wylotowej silnika rakietowego, będącej wynikiem wdrożenia autorskiej, opatentowanej technologii addytywnej LWDC (Laser Wire Direct Closeout). Prototyp z powodzeniem przeszedł wymagające próby wytrzymałościowe i temperaturowe, bezpośrednio poprzedzające zgłoszenie produktu do użytkowej certyfikacji. NASA przedstawiła pomysł jako w pełni gotowy i zdatny do komercyjnego wykorzystania.
Czytaj też: NASA zbuduje komponenty satelitów w kosmosie
W NASA Marshall Space Flight Center zapoczątkowano również badania innego rodzaju, ukierunkowane na sprawdzenie przydatności i efektywności procesu wytwarzania addytywnego w samej przestrzeni kosmicznej. W 2014 roku ruszyły eksperymenty z drukarką 3D umieszczoną na ISS. W ramach inauguracyjnych testów astronauci wydrukowali z powodzeniem w warunkach mikrograwitacji pierwsze proste narzędzia z tworzywa sztucznego. Przedmioty wydrukowane na pokładzie ISS zostały wkrótce przewiezione na Ziemię w celu ustalenia, czy kosmiczne otoczenie wpłynęło na właściwości mechaniczne lub strukturę materiału w jakikolwiek istotny sposób. W 2016 roku firma Made in Space dostarczyła Międzynarodowej Stacji Kosmicznej kolejną, ulepszoną wersję wytwornicy przystosowanej do pracy w warunkach mikrograwitacji.
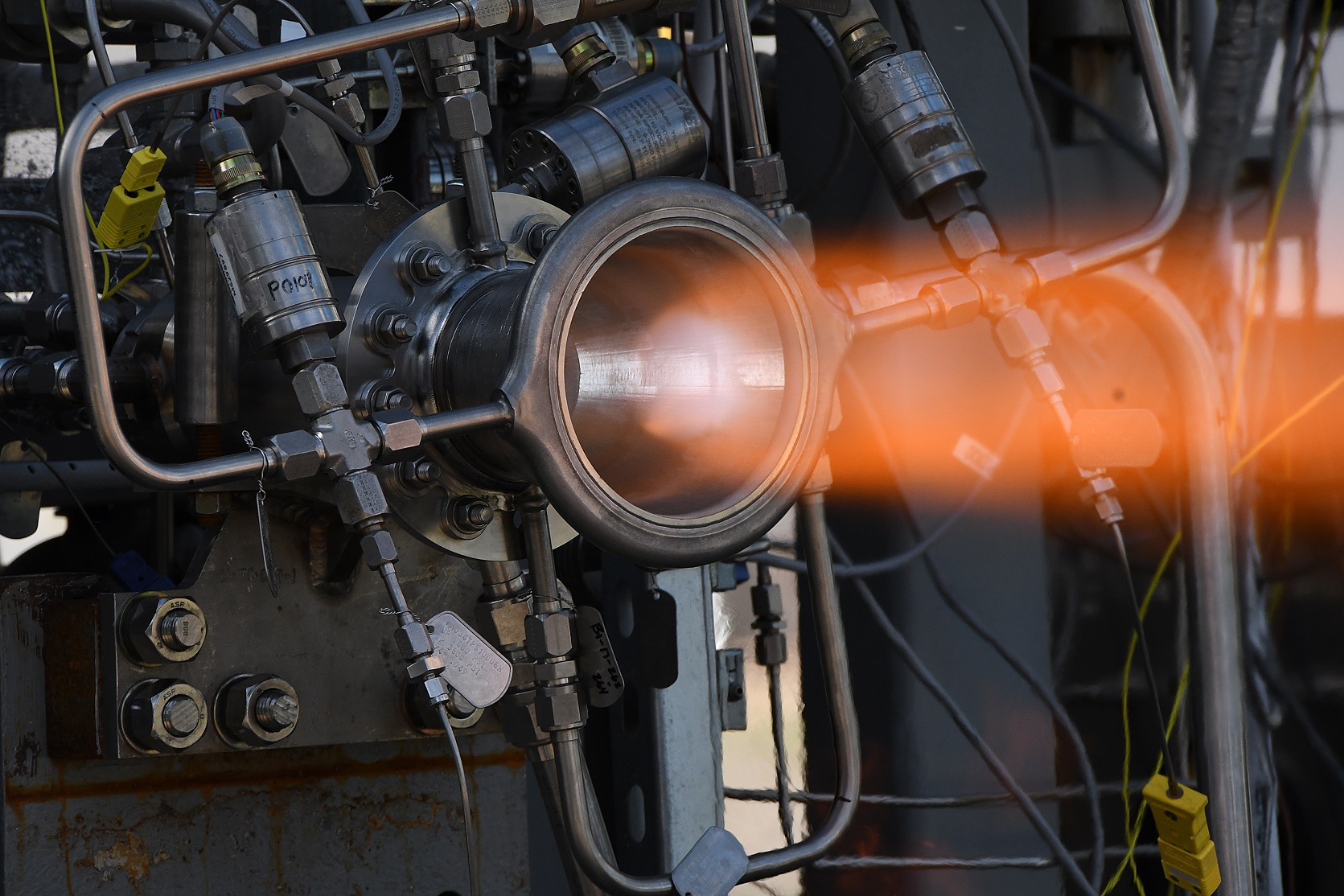
Komercjalizacja i nowe możliwości
Na niwie badawczo-rozwojowej, swój wkład w określanie sektorowej przydatności technologii addytywnych miała również Europejska Agencja Kosmiczna. W 2016 roku specjalnie w tym celu powołano do życia ośrodek Advanced Manufacturing Laboratory, działający przy ośrodku technologicznym Rutherford Appleton Laboratory w brytyjskim kampusie technologicznym w Harwell. Jako główne punkty odniesienia obrano tam możliwości zastosowania wydruków 3D w badawczych i satelitarnych misjach pozaziemskich, zarówno w wymiarze produkcji narzędzi pomiarowych, jak i elementów napędowych czy konstrukcyjnych statków kosmicznych.
Jednym z praktycznych przykładów zaangażowania ESA było badanie potencjału wytwarzania przyrostowego podzespołów napędowych dedykowanych głównie satelitom – zwłaszcza dysz wylotowych, komór spalania, a także elementów układu paliwowego. W tym celu podjęto współpracę m.in. z amerykańską spółką technologiczną 3D Systems (jednym z pionierów na rynku wytwarzania przyrostowego). Badano wspólnie m.in. potencjał użytkowy laserowych metod nawarstwiania sproszkowanego materiału budulcowego (Direct Metal Laser Sintering, DMLS).
Czytaj też: Brytyjski przemysł kosmiczny. Co po Brexicie?
Wdrażanie technologii addytywnych na prawdziwie przemysłową skalę rozkręciło się na dobre wraz z ekspansją prywatnej, komercyjnej działalności w branży kosmicznej. Postępy w tym zakresie były silnie skorelowane z poszukiwaniem dróg minimalizowania kosztów świadczenia usług astronautycznych, szczególnie w oparciu o lekkie systemy nośne oraz pojazdy wielokrotnego użytku. W styczniu 2014 roku firma SpaceX po raz pierwszy przeprowadziła własną misję kosmiczną z obecnym na pokładzie drukowanym komponentem mechanicznym. Był nim główny zawór utleniacza (MOV, Main Oxidizer Valve) obsługujący jeden z dziewięciu silników Merlin 1D użytych na pokładzie ówczesnej wersji rakiety Falcon 9.
W ślad za konkurencją postanowiła niebawem iść także spółka Blue Origin, która podjęła decyzję o zaopatrzeniu rozwijanego wciąż silnika BE-4 w turbopompy stworzone głównie w oparciu o metody przyrostowe. Oczekująca na swoją premierę w 2019 roku jednostka napędowa przygotowywana jest z myślą o startach przyszłej ciężkiej rakiety New Glenn.
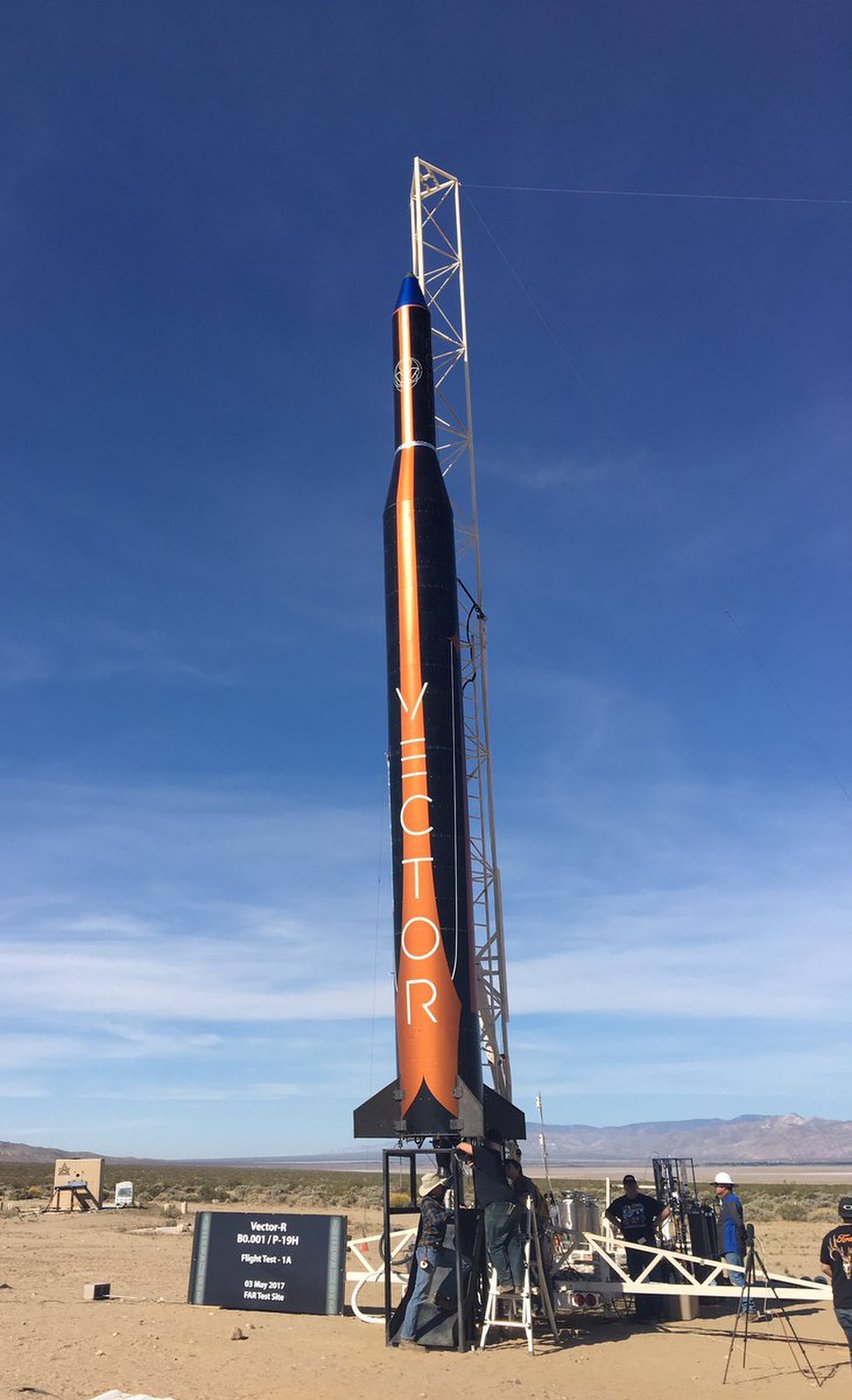
Z podobnych rozwiązań przemysłowych szybko zaczęły korzystać też inne, nierzadko znacznie mniejsze firmy i spółki branżowe. Wytwarzanie przyrostowe podzespołów napędowych stało się wręcz znakiem rozpoznawczym wschodzących spółek na rynku lekkich rakiet nośnych i drobniejszych prywatnych producentów satelitów. Drukowane przestrzennie komponenty zagościły w konstrukcjach głównych przedstawicieli sektora, czyli firmy Rocket Lab (syntetyczne zawory, turbopompy i elementy komory silnika Rutherford napędzającego lekkie rakiety Electron) oraz Vector Space Systems (wtryskiwacz paliwa w silniku pojazdu Vector, pomyślnie przetestowany we współpracy z NASA Marshall Space Flight Center w grudniu 2016 roku).
Za nimi poszły już kolejne przedsiębiorstwa sektora lekkich technologii kosmicznych, spośród których wiele prowadzi swoją działalność na Wyspach Brytyjskich, korzystając z dogodnych warunków rozwojowych z perspektywą rychłego powstania ośrodków startowych dla lekkich pojazdów. Jednym z najbardziej perspektywicznych jest szkocko-ukraińska spółka Skyrora, składająca obecnie własną niskogabarytową rakietą nośną w oparciu o podzespoły produkowane addytywnie. Pierwszy testowy lot suborbitalny pojazdu zaplanowano na ostatni kwartał 2018 roku.
Nie mniejsze zainteresowanie wytwarzaniem addytywnym wykazuje brytyjska branża nanosatelitarna. Jej wiodący przedstawiciele liczą, że rozwój w tym kierunku pozwoli na znaczące przyspieszenie i zautomatyzowanie produkcji lekkich satelitów, gwarantując powszechny i tani dostęp do nieomal seryjnie produkowanych konstelacji użytkowych. Wśród przedsiębiorstw o najbardziej szeroko zakrojonych pomysłach na wytwarzanie addytywne satelitów jest m.in. Surrey Satellite Technology LTD (SSTL). Jeszcze w 2016 roku ten czołowy światowy dostawca lekkich technologii satelitarnych przedstawił założenia wdrażanego intensywnego procesu produkcyjnego, nastawionego na pełną realizację zamówienia (od zlecenia projektowego aż do momentu wystrzelenia ładunku) w ciągu zaledwie 6-7 miesięcy. Receptę na zapewnienie odpowiedniego przemysłowego współczynnika „sprawność-koszt” dostrzeżono właśnie w metodzie wytwarzania przyrostowego komponentów satelitarnych.
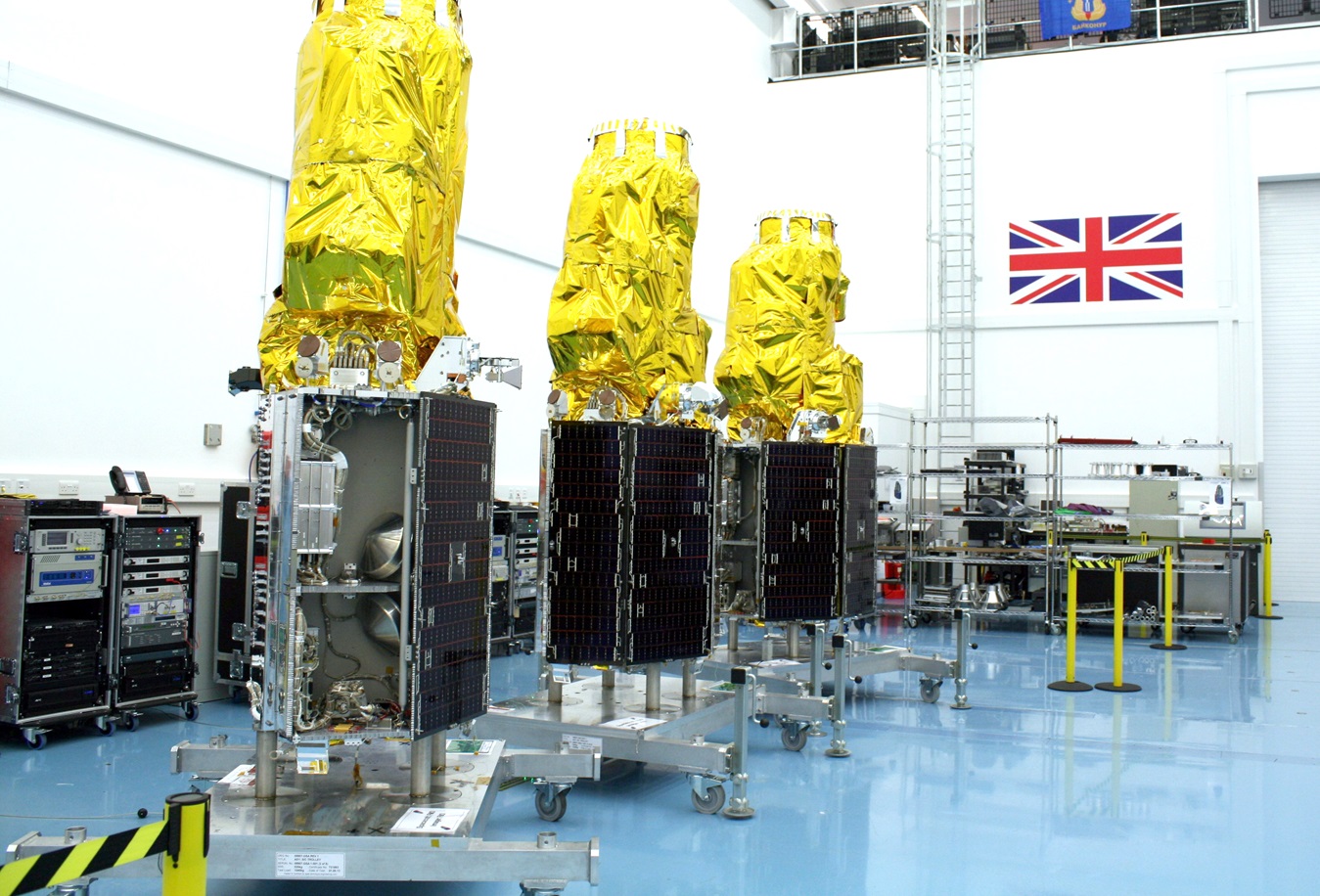
Z optymizmem w przyszłość
Przytoczone przykłady zastosowania metod wytwarzania przyrostowego to zasadniczo już codzienność funkcjonowania współczesnego sektora kosmicznego w skali globalnej. W harmonogramach realizacji najnowszych projektów branżowych widnieją już jednak znacznie bardziej zaawansowane i ambitne pomysły spożytkowania podaży technologii addytywnych. Ich myślą przewodnią jest dążenie do gruntownej zmiany koncepcji i środowiska budowania sprzętu kosmicznego. Jego podstawą pozostaje poszukiwanie rozwiązań, które wyeliminują potrzebę kosztownego i skomplikowanego wynoszenia na orbitę gotowych komponentów zmontowanych uprzednio na Ziemi.
Zakres rozpatrywanych tutaj zastosowań jest nad wyraz szeroki. Rozciąga się od pomysłów serwisowania i naprawy działających satelitów, poprzez plany uruchomienia orbitalnych, zrobotyzowanych manufaktur wytwarzających sprzęt satelitarny, aż po wizje habitatów i stacji pozaziemskich, budowanych autonomicznie z lokalnie dostępnej materii kosmicznej. Wspomina się również o możliwościach realizowania dalekiej eksploracji pozaziemskiej i misji badawczych z użyciem syntetycznych sond, wytwarzanych na miejscu u celu wyprawy przez specjalnie do tego przygotowane statki ekspedycyjne.
Jakkolwiek przez wzgląd na wciąż niedostateczny poziom zaawansowania technologii są to cele i zdolności czysto hipotetyczne, w wielu tych zakresach trwają już studia wykonalności i procesy oceny potencjału realizacji. Zamysł wykorzystania metod drukowania 3D stanowi obecnie integralną część planów ekspedycji międzyplanetarnych i zakładanej kolonizacji Księżyca i Marsa. Naturalnym celem pośrednim (i relatywnie najbliższym osiągnięcia) pozostaje w tym kontekście uzyskanie zdolności do autonomicznego wytwarzania narzędzi i części zamiennych w kosmosie. Samo to już jednak powinno stanowić punkt zwrotny w przedmiocie określania granic operacyjnych, czasowych i przestrzennych realizacji misji kosmicznych.
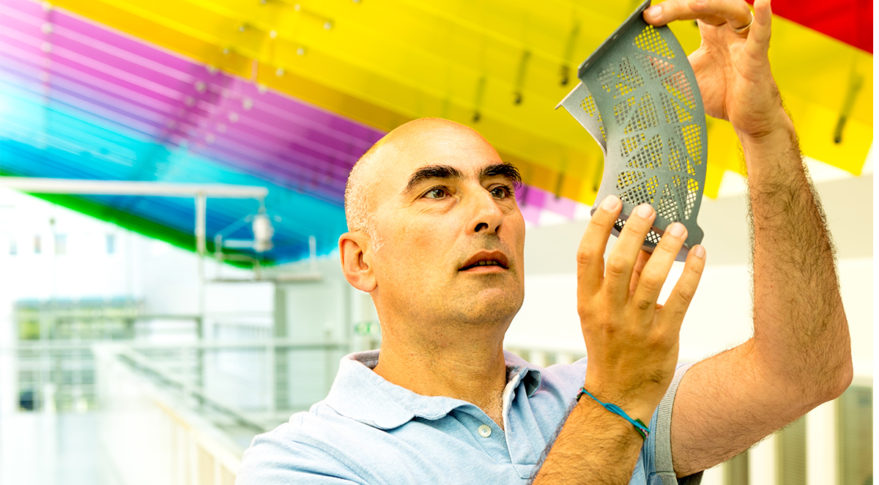
Wiele o ogólnych możliwościach i dynamice postępu ukierunkowanych na ten cel działań mówią projekcje formułowane przez technologów materiałowych ESA. Jeden z nich, Laurent Pambaguian, z optymizmem odnosi się do oczekiwanych postępów w dziedzinie wytwarzania przyrostowego na potrzeby eksploracji kosmicznej. „Obserwujemy gwałtowne zmiany w globalnym krajobrazie technologii produkcyjnych. Praktycznie co dwa miesiące pojawia się nowy producent [sprzętu addytywnego – przyp. red.], a co sześć miesięcy powstaje nowa technologia [wytwarzania przyrostowego – przyp. red.] i są rozwijane nowe stopy materiałowe” – stwierdza. Biorąc to pod uwagę, Pambaguian oczekuje, że pierwsze wyprodukowane addytywnie podzespoły znajdą się na pokładzie satelitów ESA w perspektywie 4-5 najbliższych lat. Dotyczy to jednakowo składników napędowych, mechanizmów sterujących, a nawet elementów elektrooptycznych. ESA ma być również już obecnie zaangażowana w badanie technologii pozwalających na wsparcie konstruowania tzw. wioski na Księżycu.
Póki co jednak najbardziej realny i namacalny postęp obserwowany będzie nadal w dziedzinie wytwarzania struktur napędowych rakiet nośnych i systemów aeronautycznych. Przewiduje się, że przy produkcji prototypów kompletnych silników do roku 2020 ponad 50 proc. ich części będzie już wykonywanych w technologii przyrostowej. Producenci tacy, jak GE Aviation będą skupiać się na radykalnym ograniczeniu liczby osobnych komponentów i całkowitej masy jednostek napędowych. Można też liczyć na to, że w krótkim czasie wspomniany trend zostanie zaobserwowany, choćby w pewnym zakresie, także w branży astronautycznej.